Interview with outside directors
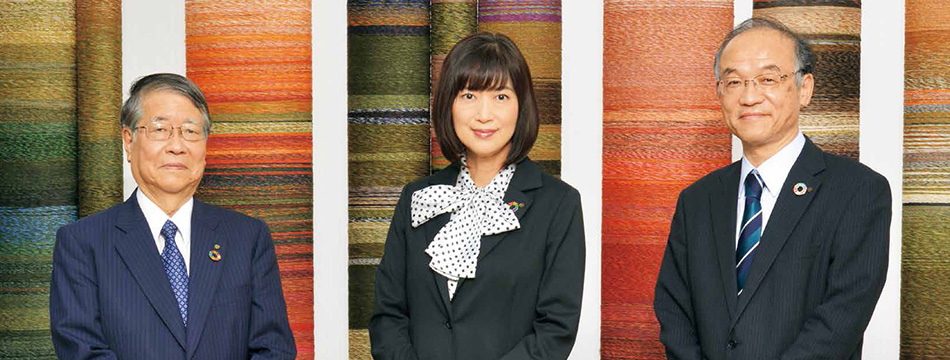
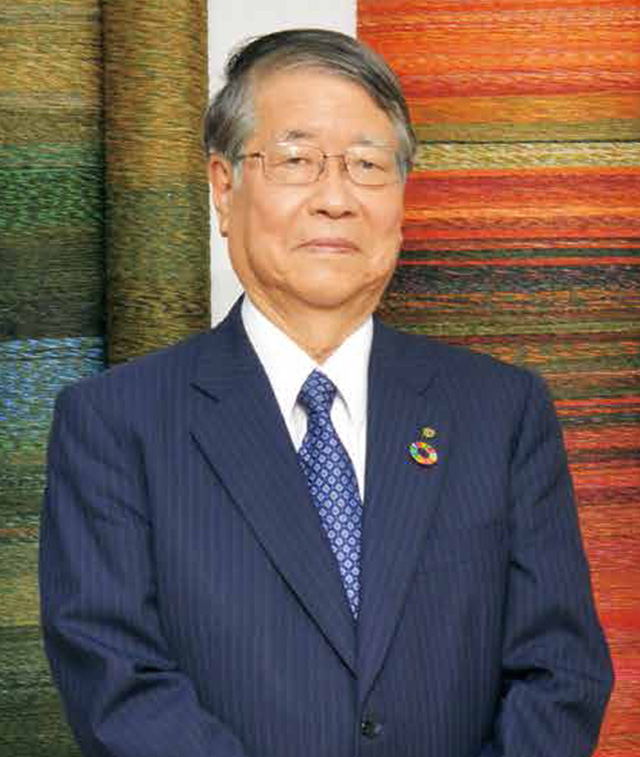
Sojiro Tsuchiya
Career summary
Toyoda Gosei director since June 2015
Formerly executive vice president of Denso Corporation
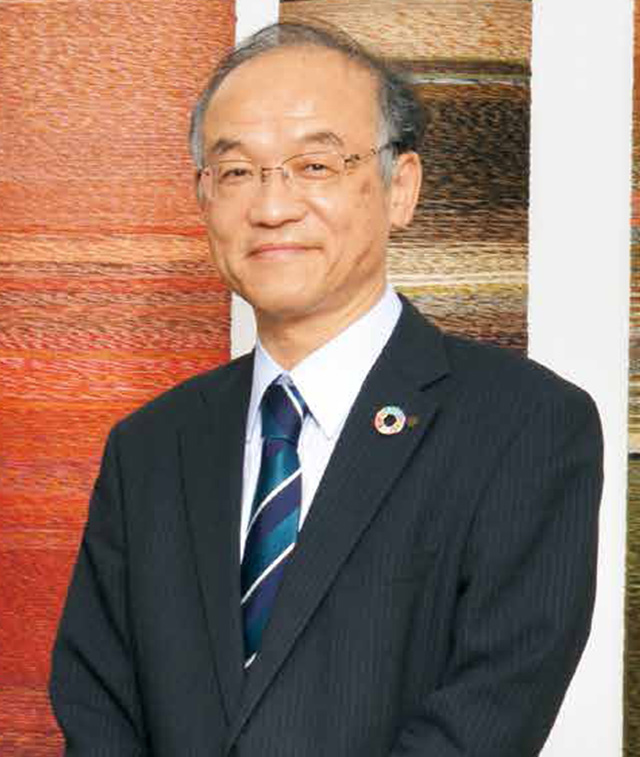
Mayumi Matsumoto
Career summary
Toyoda Gosei director since June 2019
Visiting Associate Professor, Special Division of Environmental and Energy Science, Komaba Organization for Educational Excellence (KOMEX), The University of Tokyo (current)
Kimio Yamaka
Career summary
Toyoda Gosei director since June 2016
Director, Energy Strategy Institute Co., Ltd. (current)
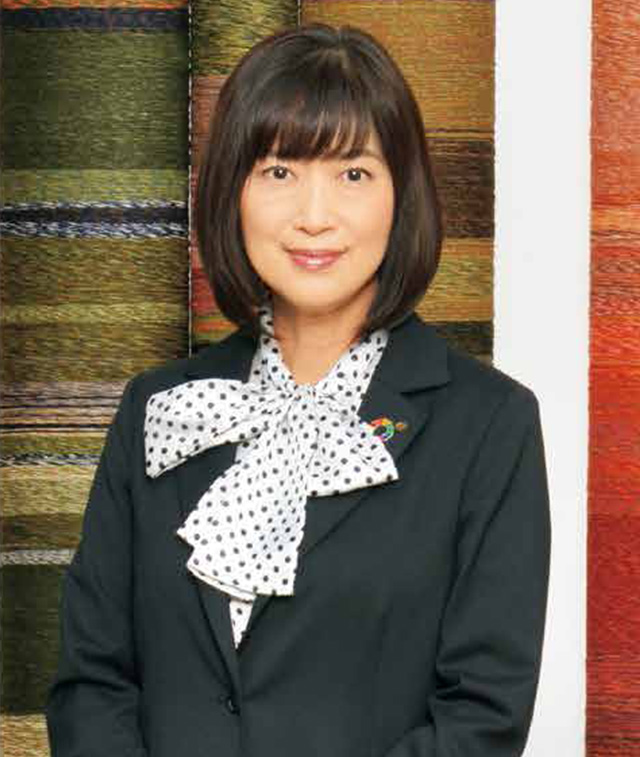
Kimio Yamaka
Career summary
Toyoda Gosei director since June 2016
Director, Energy Strategy Institute Co., Ltd. (current)
Mayumi Matsumoto
Career summary
Toyoda Gosei director since June 2019
Visiting Associate Professor, Special Division of Environmental and Energy Science, Komaba Organization for Educational Excellence (KOMEX), The University of Tokyo (current)
Outside directors’ roles
TsuchiyaTo ensure transparent Board decision-making, I place priority on providing objective advice based on my knowledge and experience. Having worked for another manufacturer like Toyoda Gosei, I am communicating with front-line personnel as much as possible and offering context-specific advice from an outsiders’ perspective to help them to properly fulfill their roles.
YamakaI am committed to unreservedly expressing opinions from stakeholders' standpoint to fulfill my role of monitoring and advising management so they can benefit from my expertise and experience.
MatsumotoSince first becoming a director, I have focused primarily on the monitoring function in light of the company’s circumstances and investors’ needs. With outside directors assuming increasingly important responsibilities, I actively question whatever I find questionable and speak out as an advocate for regular shareholders.
Progress in corporate governance
TsuchiyaSince I joined the Board, Toyoda Gosei has made great strides in terms of corporate governance by virtue of growing societal interest in governance in addition to the company’s efforts. I feel Toyoda Gosei stacks up well against other Japanese companies with respect to governance.
YamakaWe are steadily upgrading our monitoring regime. I believe we are sensitively responding to the demands of the times. To function effectively, however, outside directors need a deeper understanding of the company’s business activities. I would like to be briefed in even more detail than we are now.
MatsumotoWhile Mr. Yamaka has been a director for four years, I joined the Board just last year. In contrast to four years ago, when outside directors reportedly had few opportunities to learn about the company, I have had numerous opportunities to do so, including through plant tours and studying about business activities before officially being appointed. Given the gravity of outside directors’ responsibilities, I appreciate that Toyoda Gosei not only provides opportunities to learn but also promptly answers questions and responds to requests.
Board’s effectiveness and shortcomings
TsuchiyaI think very highly of the Board. Board meetings have a good atmosphere conducive to candid discussions. I believe discussions among people with diverse experience and backgrounds are extremely important. It would be better to have broader discussions with input from more perspectives, including not only management and governance but also product technologies, production, quality, sales and service.
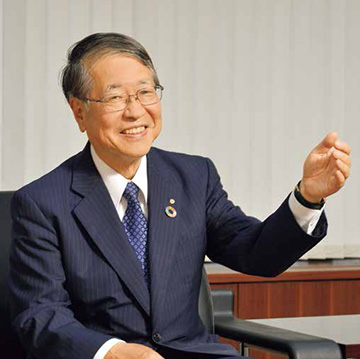
YamakaI feel we outside directors contribute to lively discussions because we mostly speak candidly. The Board often makes decisions on information-intensive matters under tight time constraints. I sometimes would like to be able to devote more time to discussion. Allocating discussion time among agenda items is a tough balancing act, but I wish the Board would put a bit more thought into doing so.
MatsumotoAs a newcomer, I initially had a hard time understanding what was being discussed at times. Management helped me to become an effective director by, for example, inviting me to Production Meetings and Sales Meetings so that I could learn about the company’s medium- to long-term direction. I strive to arrive at optimal solutions by personally taking the initiative to learn what I need to know and clearing up any questions.
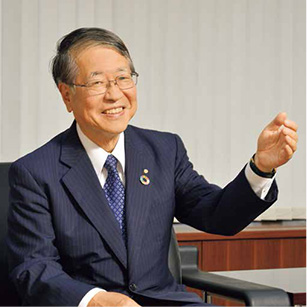
Toyoda Gosei’s key management issues
TsuchiyaWe are said to be in a once-a-century period of monumental change. With autos also undergoing drastic change, what we produce is becoming increasingly important together with how we produce it. Technological capabilities are now more crucial than ever before. To reliably meet customers’ needs and wishes, we must develop various new manufacturing technologies even for decorative interior and exterior components, for example.
Information and electronic technologies are likewise becoming essential in the safety/security and autonomous driving domains. It is important for Toyoda Gosei to create innovative new value by combining the LED technologies it has long been refining with materials technologies, another of its fortes. Identifying products and businesses that will drive Toyoda Gosei’s growth going forward and allocating management resources to them on a priority basis are currently two key management issues in my opinion.
YamakaThough many people in the company think good technology directly leads to sales increase, it is important to be cognizant of how to best embody technologies in products and how to generate profits from technologies. With the auto industry changing drastically, customer stability can no longer be taken for granted. In such an environment, I believe shifting to a mentality of self-reliance vis-à-vis generation of both ideas and profits is a key issue.
For example, Toyoda Gosei has been lauded for its environmental initiatives. Environmentally friendly products not only generate stable profits, they also constitute a promising domain in which to create new businesses by leveraging existing technologies. A hydrogen society extending beyond FCVs will definitely be realized at some point and the inverter model of energy transmission/control will become mainstream.
MatsumotoTechnological development is the linchpin of Toyoda Gosei’s businesses. Given the necessity of developing products that are attuned to the needs of the times and address societal challenges, it is important to put products out into the world on a pilot basis from an early stage. Short-term risks should definitely be taken in pursuit of growth, but needless risks must be controlled. I believe greater risk-sensitivity is needed. Over the medium to long term, I think Toyoda Gosei should engage in dialogue with not only existing partners but also young digital natives that will form the nucleus of the next generation to learn more about what kind of cars they are seeking and what kind of society they want to live in, as well as needs and vehicle features in the autonomous driving era. Such information should be utilized in product development.
TsuchiyaI am glad we decided to divest German subsidiary TG Meteor. The move largely resolved a big problem. It was a big decision for the company and a lot of hard work but, thankfully, the deal closed successfully. On the whole, the interior and exterior components business and safety systems business, particularly airbag-related products and millimeter wave compatible emblems, are growing steadily and expected to continue to grow. The rubber components business is not doing so well, but it is Toyoda Gosei’s original business and its products are essential automotive components. It must somehow be turned around into an attractive business again. Morimachi Plant personnel are currently working together to steadily improve operations and develop technologies. I am confident their efforts will produce impressive results in the near future.
Amid the current pandemic, I am a bit concerned about the company’s global production network. Labor-intensive production processes like sewing airbags and wrapping steering wheels in leather are concentrated in countries like Vietnam from the standpoint of both labor availability and labor costs. We have to think about not only the current pandemic but also abnormal weather events such as floods, which have been increasing in severity in recent years, and natural disasters such as earthquakes, tsunamis and wildfires in addition to other risks such as labor disputes. While geographic concentration of certain operations undeniably has major efficiency benefits, I see the pandemic as a reminder that we need to think about how to balance such benefits against the risks of overconcentration.
Yamaka With Toyoda Gosei supplying a wide range of products globally, the words “One Team, One TG” resonates with me more deeply with each passing year. Despite the expectations placed on the company, setbacks sporadically occur due to what I consider to be company-wide communication deficiencies. I believe it is crucial to have a mindset of working together and generating profits in unity, irrespective of their business domains, positions or roles.
Branching into new domains, including not only the CASE space but also non-automotive businesses, will also be important. In automotive businesses, we basically aim to recoup investments over five-year intervals. In other sectors, however, our approach differs by sector. I feel that Toyoda Gosei has plenty of human resources capable of adapting to new environments. For example, the environment and energy staff have grown tremendously over the past four years to the point where I now sometimes learn from them.
Advancement of production engineering
TsuchiyaProduction engineering is on a good trajectory but it does not exist in a vacuum. It is one component of manufacturing. Its full power is unleashed only when it is integrated into the process from development and design through production and sales. If a production plant is thrown out of kilter by the introduction of an incompatible product or process, the incompatibility will lead to quality and profitability problems. Manufacturing entails not only production engineering and a production site but also coordination and cooperation among the manufacturer’s entire workforce. Production engineering’s role includes coordinating all activities central to manufacturing.
I believe Toyoda Gosei’s production engineering program has been getting stronger and making steady progress in various improvement activities and new development projects. It is important to have a strategy for extending the program globally and on a Group-wide basis to allow it to directly contribute even more to improving competitiveness and profitability.
Comments as chairperson of executive appointment and executive compensation committees
Yamaka I feel the magnitude of my responsibility as committee chairperson, a critical role related to the company’s management. I aim to make sure committee members can engage in candid discussions from an outsider’s vantage point at meetings. To ensure impartial, independent and appropriate decisions, I plan to provide opportunities to communicate with a wide range of individuals and promote understanding of policies.
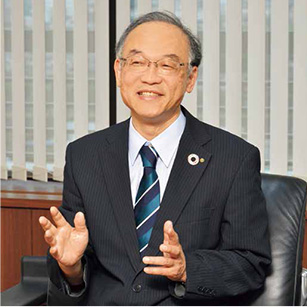
SDGs and ESG activities
MatsumotoBecause Toyoda Gosei’s SDGs are grouped together, I was initially unsure how they translate into action. This year, I did a materiality reassessment, which was a big step forward in the space of one year. I value the opportunity to personally educate employees at workshops and other places on SDGs that enable them to individually contribute to society while doing their jobs.
TsuchiyaAs members of society, companies are naturally obliged to take ESG seriously. Both commitment and technology are essential to realizing ESG objectives. I believe Toyoda Gosei can greatly contribute technologically given its wide-ranging technological capabilities.
YamakaIn terms of the environment, one of the pillars of ESG, Toyoda Gosei has been discussing methodologies and progressing toward long-term targets with deadlines of 2030 and 2050. Rapid advancements in energy efficiency and renewable energy are heavily influencing its new product and new technology strategies also. I expect such a comprehensive strategy to help drive growth for “environmentally friendly TG.”
Diversity
MatsumotoGiven the nature of Toyoda Gosei’s business as an auto parts manufacturer, most of its workplaces are staffed with more men than women, but it is consciously hiring more women. In terms of diversification of work styles, telecommuting, which was previously limited, has expanded throughout the company in response to the COVID-19 pandemic. Even after the pandemic ends, I hope the company continues to allow telecommuting as a means of increasing employee retention.
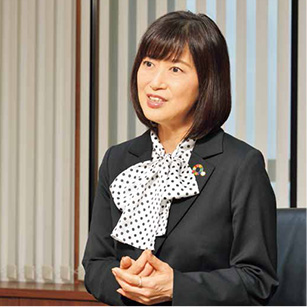