Building a Decarbonized Society
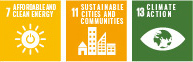
In addition to lighter weight products that lead to improved vehicle fuel efficiency, we are reducing CO2 emissions through improved productivity and more efficient distribution.
Basic philosophy
In addition to achieving the goal set under the Paris Agreement of keeping the rise in the global average temperature to below 2℃ compared with pre-Industrial Revolution levels, we must reduce greenhouse gas emissions to virtually zero by the end of this century. With the aim of zero CO2 emissions as presented in the TG 2050 Environmental Challenge, we are utilizing new production techniques and product development skills with an eye toward next-generation vehicles in addition to the manufacturing skills we have cultivated over time. Plans for execution are included in our 7th Environmental Action Plan with activity targets for FY2025. We have also set the goal of cutting CO2 emissions 50% (vs FY2013 levels) by 2030, the midpoint for the TG 2050 Environmental Challenge, and implementing stepwise, specific CO2 reductions. We are also conducting activities to reduce CO2 emissions over the entire life cycle, with consideration of parts and materials procurement, product development, production, and use up to the disposal stage. In June 2021 we started a company-wide, cross-sectional carbon neutrality project to accelerate these activities.
Reducing CO2 emissions
The Toyoda Gosei Group is reducing CO2 emissions in the product stage, production stage, and over the entire lifecycle to achieve the targets set for FY2025.
Product development stage: Environmentally-friendly product development
In the product stage, we are making headway in providing parts for environmentally-friendly, next-generation vehicles and developing products with lighter weight for greater fuel efficiency and lower energy consumption across the areas of materials technology, product design, and production technology. Examples include the development of hydrogen tanks for FCEVs and aggressive efforts to switch materials (e.g., from metal or rubber to plastic) in instrument panel peripherals and other interior products and in functional parts such as hoses, reduce the number of components, integrate functions, and use thinner material while ensuring strength.
Large plastic roof panels for fuel cell buses
We have succeeded in switching from metal to plastic for lighter weight in the large roof panels placed over fuel cell stacks and high pressure hydrogen tanks. It used to be that metal had superior strength, but we have developed plastic material that contributes to lighter weight with reduced thickness while maintaining impact and heat resistance levels. We have also been able to reduce the weight of large parts with no loss of function, by using technology that forms the products with uniform thickness and high accuracy. We intend to expand this to similar products in the future.
Production stage: Reductions with development of new processes, daily kaizen
We have set 2030 milestones for achieving zero plant CO2 in the TG 2050 Environmental Challenge, and are working to achieve this with regular kaizen, production technology innovations, more efficient utilities, and expansion of renewable energy in plants.
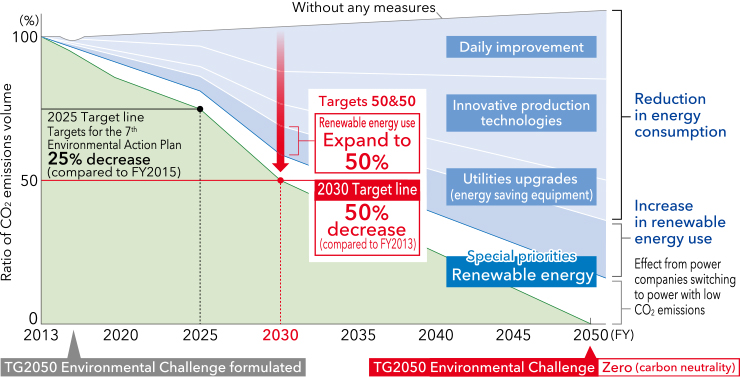
Switching fuel for boilers and hot and cold water generators from kerosene to LNG and heat pumps
Carbon emissions at the Seto Plant have been decreased by installing liquefied natural gas (LNG) equipment and switching fuel for boilers and hot and cold water generators to LNG and heat pumps. In addition to huge reductions in CO2 emissions by changing from kerosene to LNG and heat pumps to power heating and cooling equipment, this has also led to decreases in sulfur oxides (SOx) and nitrogen oxides (NOx), which are causes of air pollution.
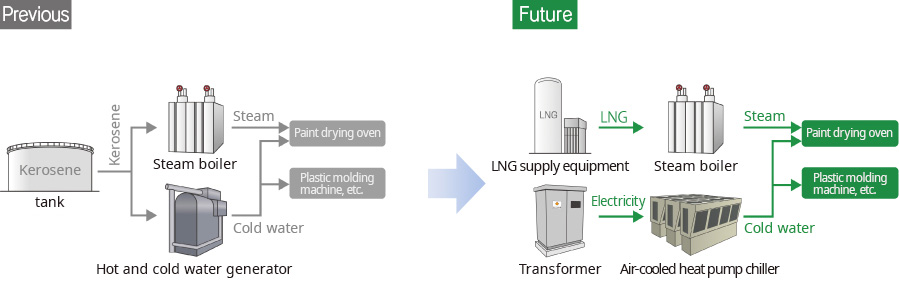
CO2 emissions, CO2 emissions per sales unit (index) *1
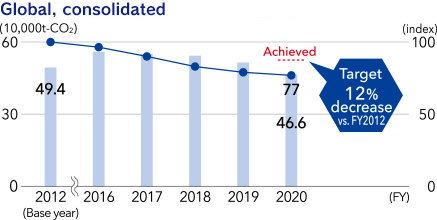
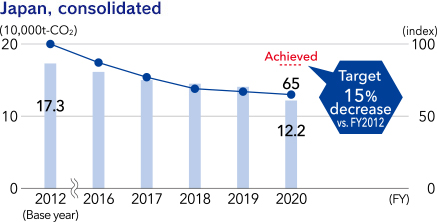
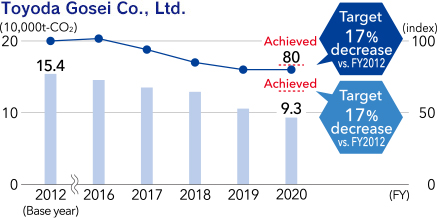
- *1 Emissions per sales unit (index) is a figure obtained taking FY2012 as 100
- [CO2 conversion factor]
The CO2 conversion factors used for Japan*2 are the 1990 Keidanren factors. The CO2 conversion factors used for other countries are from the GHG Protocol (2001). - *2 Electricity: 0.3707t-CO2/MWh, class A fuel oil: 2.69577t-CO2/kL, LPG: 3.00397t-CO2/t, Town gas: 2.15701t-CO2/1,000 Nm3, Kerosene: 2.53155t-CO2/kL, LNG: 2.68682t-CO2/t,
Gasoline: 2.36063t-CO2/kL (excluding external factors of gas companies’ town gas heat conversion)
Recycling: Reductions in materials and parts procurement, more efficient distribution
Toyoda Gosei has prepared and distributed green procurement guidelines for materials and parts procurement with low environmental impact. Together with regular supplier surveys to ensure compliance, we also provide support when improvements are needed.
We have reduced CO2 emissions with more efficient distribution, including truck allocation with improved payloads and shorter distribution distances and reviews of transport modes.
■CO2 emissions in distribution, CO2 emissions per sales unit (index)*1
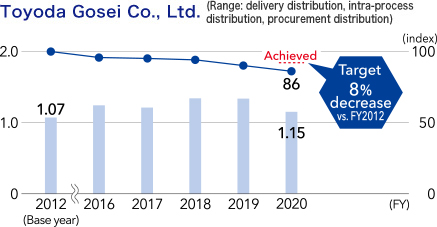
Renewable energy
We are expanding renewable energy, including the installation of clean solar and wind energy generation equipment and the purchase of green power. This reached 4% of our total global electricity consumption by the end of FY2020, more than meeting our target of 2%. Our next challenge is to raise clean energy levels to at least 20% globally by FY2030.
■Solar power generation graph (does not include stand-alone systems such as outside lights with solar panels)
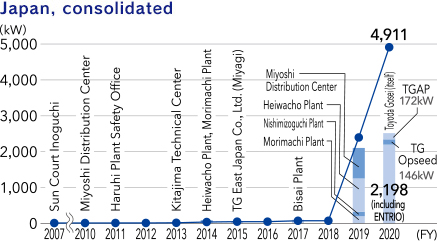
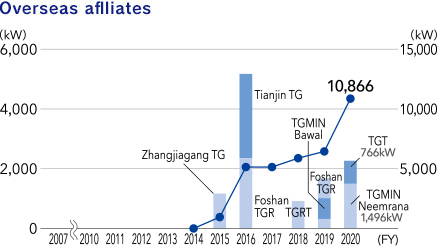
Solar power generation system installed at TGRT
A solar power system with a generation capacity of 915kW was installed at TGRT in Thailand. This is equivalent to 8% of the electricity purchased by TGRT, and has the effect of reducing CO2 by 760 tons annually.
Wind power system and geothermal air conditioning system at the Inabe Plant
The Inabe Plant has installed a wind power generation system (10kW) and geothermal air conditioning system. We are also planning to install solar power generation and other equipment.
Reductions in 6 greenhouse gases*3
Of the six greenhouse gases, Toyoda Gosei Co., Ltd. uses three (HFC, PFC, SF6) and is conducting activities to reduce all of them. By FY2015 we had completed a switch to alternative gases with a low environmental impact for the shield gas used in the production of steering wheel cores and other gases. This has resulted in a 74% decrease in greenhouse gases since FY2012. We will continue these reduction activities in the future.
- *3 Hydrofluorocarbon (HFC), perfluorocarbon (PFC), sulfur hexafluoride (SF6), methane (CH4), nitrous oxide (N2O), nitrogen trifluoride (NF3)
■Trend in greenhouse gas (6 gases) emissions (CO2 equivalents)
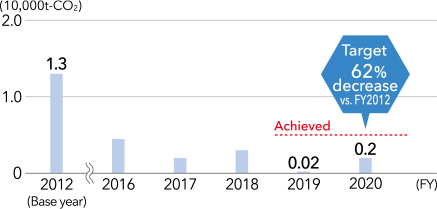
Contributions as a pioneer in environmentally-friendly LEDs
Development and spread of products that use LEDs
Toyoda Gosei is making progress in improving the quality of light, from light that is merely visible to light that brings out the charm of things, with the development of sunlight LEDs that approach a color tone close to that of sunlight and other developments to show objects including human skin and commercial products at their most natural and appealing. To make our attractive LED technology and products more widely known, we participate in domestic and international exhibitions and events and are working to encourage the spread of LEDs.
Development of air conditioner register with LED lighting
Development of air conditioner register with LED lighting
We have developed an air conditioner register with LED lighting incorporated into the knob that adjusts the direction and strength of air flow. This improves the nighttime visibility of the knob. Wireless power transfer technology*4 is also applied to avoid previous concerns such as wire harness breakage from repeated manipulations of the knob. Together with improved nighttime manipulability, the LED register also contributes to a futuristic and elegant interior mood, while use of an LED light source helps to reduce energy consumption.
- *4 Using the physical phenomenon of resonance, in which a vibrating system drives another system to oscillate at specific frequencies, the technology enables the transfer of electric power to a distant location by causing resonance in the frequency of the magnetic fields among resonant circuits.
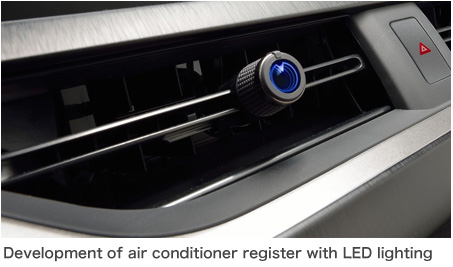
- Contributing to Environmental Preservation Through All Our Business Activities
- Environmental Action Plan
- Building a Decarbonized Society
- Building a Recycling Society
- Environmental Preservation and Building Environmentally-Friendly Societies
- Environmental Management
- Collaboration with External Organizations
- Environmental Efforts at Affiliated Companies
- Environmental Data
- Third-Party Verification
- TCFD
- Third-Party Assessment