Relentless effort is needed in manufacturing areas to ensure competitiveness and grow sustainably as laws and regulations are strengthened to combat global warming, competition intensifies with the advent of CASE, populations in developed nations age, labor costs in developing nations rise, and other changes occur in the environment.
The “TG Advanced Factory Concept” was formulated as our vision for the company in the future. It adds three concepts to the high productivity “Smart Factory” that has been cultivated based on the Toyota Production System. The first is that of a “Virtuous factory” that eliminates human error with the use of DX other approaches. Processes that utilize IoT and AI to prevent the generation or passing on of defects and do not cause difficulties for our customers will be achieved. Our aim is for plants where a culture of 100% compliance with laws and regulations has taken root and our colleagues around the world can work in safety. Second is the concept of a “Clean factory” that makes full use of innovative production technologies. As we work toward achieving carbon neutrality by 2050, we will continue activities to reduce CO2, such as reducing energy loss with process innovations, upgrading to more efficient equipment, and introducing renewable energy. In addition, we will work to develop recycling technology for rubber, which has been considered difficult to recycle, and the completely new energy technology of replacing fuels by using CO2 methanation and hydrogen. Third is the concept of a “Factory where everyone can work with vigor.” Workers are freed from burdensome tasks with the introduction of automated guided vehicles (AGVs) and expanded use of automated visual inspections and robots, and can shift to tasks with higher added value such as equipment maintenance and kaizen. This not only improves productivity, but also helps to bring about diversity so that everyone, regardless of age, gender, or other attributes can work in the same workplace with a sense of satisfaction. Currently, we are making use of this in the reorganization of production layouts under consideration in Japan as well as China and North America. In addition, we will start up new plants centered around the thinking in the TG Advanced Factory Concept.
It has been more than 40 years since Toyoda Gosei established its first overseas operations. We have accumulated local know-how and have progressed with mutual exchanges in technology and knowledge that are the strengths of each location. In 2020, we started the Global Production Liaison Committee and worked to speed up the entire group, such as by sharing information and the technology of each plant in a common database and strengthen manufacturing. In the future we will operate all the plants in the Toyoda Gosei Group that are spread across the globe as one huge factory, and develop further with the “TG One Factory Concept” that dramatically raises QCD as the ideal.
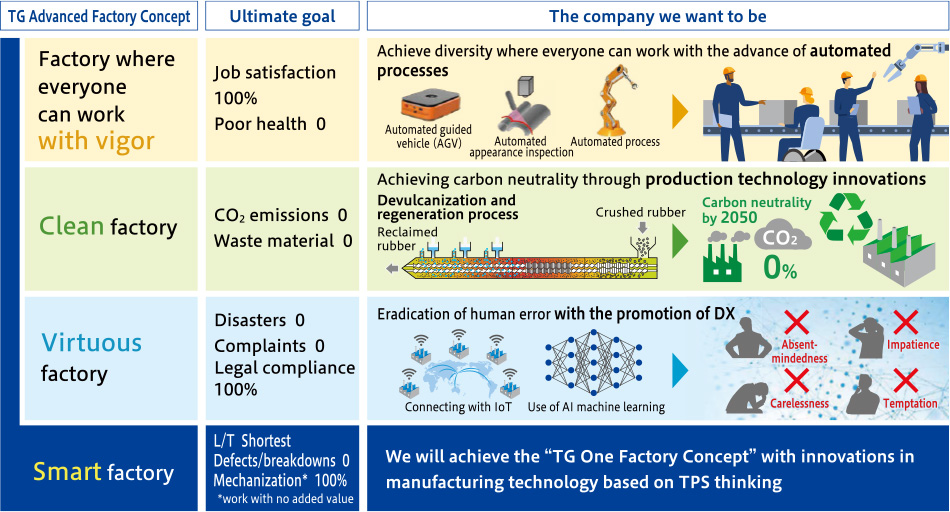
Work process innovation using IoT and AI
Elimination of defect losses is directly linked to being a factory that does not produce complaints. In cases of weatherstrip production processes, IoT technology and AI are used and lead to defect prevention measures and improvements. In addition to the experience of highly skilled workers, conducting big data analysis of all processes will help to identify factors in defects that could not be discovered with conventional kaizen methods and lead to anti-defect measures. In the future, we aim to develop control technology in which AI classifies factors in defects with high precision without going through humans, and provide automatic feedback on conditions that always produce good products. We also aim to eliminate factors caused by human error and create “virtuous factories” that do not cause problems for customers or society.
■Weatherstrip production process (use of IoT and AI)
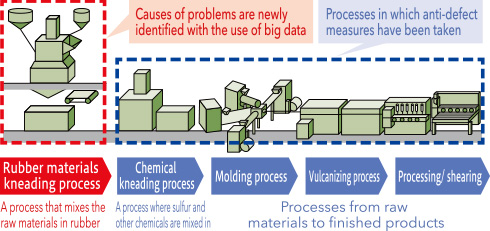
■Prevention of defects with automatic feedback control technology
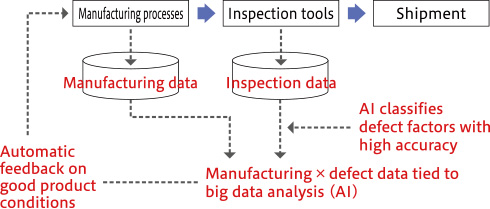
Full-scale operation of rubber recycling processes to achieve the medium-term goal of reducing waste
We aim to reduce waste materials by 30% (compared with FY2012 levels) by 2030 on our way to achieving carbon neutrality in 2050. In April 2021, recycling processes for four types of weatherstrips were brought together in a dedicated building. By restoring waste rubber to a raw material state with our original technology and using it in new products, we expect to reduce waste by about 6,000t. This should also have an effect in reducing CO2 emitted during raw material transport and the incineration of waste. In addition, we hope to contribute to reducing the environmental impacts of the industry overall, by using this recycled rubber not only in-house but also selling it to other companies.
■Weatherstrip recycling process
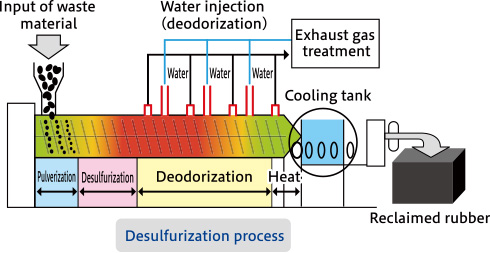
Expanding the use of robots to save labor
In starting up new production lines, we seek product specifications from the design stage that will make automation easier and aim to achieve production lines that are totally automated, from component and material input to shipment of finished products. For existing lines, we will make full use of TPS kaizen methods to separate and group tasks that can only be done by humans and all other tasks, and achieve labor-saving lines that combine collaborative robots and karakuri kaizen with low investment.
■Labor savings with automation of existing lines
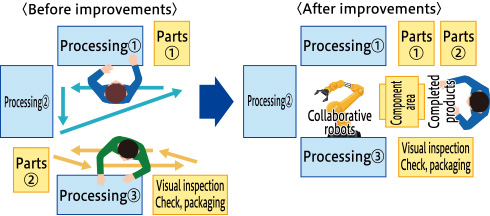