Customer Relations
With priorities on customers and quality, we are working to constantly improve our products and services and our value as a company.
Uniform global quality assurance
Toyoda Gosei ensures quality in all business activities, from development to production, based on our basic quality policy. Every one of our plants has obtained certification in the ISO 9001 (JQA QM7318/QMA11826/QMA12841) and IATF16949 (JQA-AU124) international standards for quality management systems. Each plant also sets its own quality control goals for production. These goals are based on the principles of Total Quality Management, or TQMーactivities designed to enhance the quality of products, work, and management, and increase the dynamism of individuals and organizations, through constant improvement and the participation of all based on the “Customer First” principle. In addition, all Group companies use our Quality System Global Standards, which incorporate quality improvement with rules and know-how to ensure quality.
■Fundamental principles of TQM
Monitoring and responding to manufacturing processes and market quality
Defect-free process completion is carried out in production and other processes for parts involved in the basic automotive functions of running, turning, and stopping, as these parts are directly linked to safety. We want the Toyoda Gosei name to equal quality in the minds of customers worldwide. For this purpose, we advance quality assurance declaration activities at all production locations. This means that all employees make efforts to improve safety and the people in charge of all manufacturing processes improve quality through the development of people and processes. When a mechanism that can ensure the target quality has been completed and is in place, the manager makes an “assurance declaration” to the president or site manager. The president or site manager then conducts a site inspection. Through “jidoka ,” we improve quality by creating processes that do not produce or pass on any defects and developing workers with a high sensitivity to safety and to avoiding mistakes. Audits and improvements by certified auditors of production processes for safety-related parts are also carried out.
A system is in place so that whenever a quality problem occurs in the market, we can quickly investigate the causes based on information from automakers and implement prevention measures. When it is difficult to pinpoint the cause of a problem and develop solutions internally, we work with the quality departments of automakers to take precise measures to prevent recurrence based on inspections with test vehicles and other means. In this way we prevent such quality defects from occurring in the next products.
Ongoing “Quality Assurance Declaration Activities”
We cultivate a workplace culture of continuous improvement, and “Quality Assurance Declaration Activities” have been conducted since 2012 with the aim of creating manufacturing floors with a solid manufacturing foundation that can cope well with changes. We have also begun kaizen activities with the participation of all employees based on the three pillars of Developing human resources, Developing processes, and Preventing recurrences.
From FY2021 this has evolved into an activity to measure site and workplace strengths and make improvements for the continuation of zero defects, and the company works together as one so that we can delivery safe and reliable products to customers around the world.
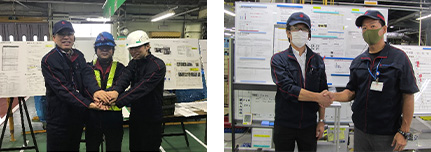
Quality Learning Center established to cultivate a quality mindset
All members of the Toyoda Gosei Group, including suppliers and international locations, learn repeatedly about quality. We have established a Quality Learning Center to cultivate a mindset of thinking and acting with a customer-first and quality-first approach. In addition to showing examples of past problems, exhibitions convey the company history of placing importance on quality, examples of quality improvements implementing the TG Spirit, and efforts for the future.
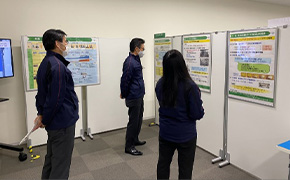
TQM for a stronger, better company
TQM activities are undertaken across the company to raise product and work quality and individual and organizational vitality, and to create a flexible and resilient corporate character through constant improvement and the participation of all based on the “Customer First” principle.
In addition to Workplace Management kaizen Activities and Small Group Activities, we are sequentially introducing education to help workers acquire AI and big data analysis skills and ways of thinking to enhance creativity, so that they can deal with a dramatically changing environment. We are also fostering a corporate culture of cultivating data literacy and wide-ranging imagination, and developing people who can contribute to DX and other transformations and to increased competitiveness.
Globally, we are energizing small group activities together with each location, focused on the China and ASEAN regions. We began a Global Small Group Activity Competition in 2016 for Toyoda Gosei companies to help each other improve.
■TQM activities at Toyoda Gosei
Level | Activities |
---|---|
Manager | Workplace management kaizen activities |
Office, technical workers | Small group activities (group kaizen activities) Activities to improve practical abilities (engineering work) in statistical quality control (SQC) and artificial intelligence (AI) |
Skilled workers | Small group activities (QC Circle activities) |
Development of data science personnel
To deal with the changing environment of recent years, such as CASE and MaaS, we have been training data science professionals since 2017. In times like today when the future is difficult to read, the TQM principle of “continuous improvement” needs to be changed to “moving from improvement to innovation and reform and innovation.” With the utilization and application of big data and the rapid expansion of DX, data science has become a necessary skill. While continuing personnel development with in-house training, we are also making efforts to collaborate in education outside the Toyota Group through industry-academia collaboration.
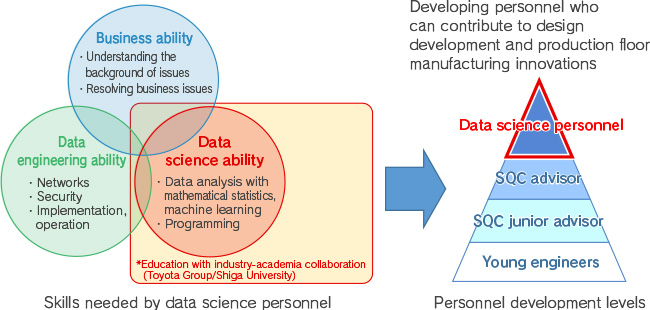
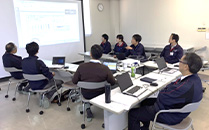
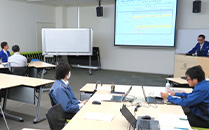
(in-company)
7th “China TQM Conference” held
In China, where recovery from the coronavirus epidemic came relatively early, small group activity conferences have continued. The sixth conference was held online in 2020 and the seventh conference was held in person in the Zhangjiagang area in 2021.
From the seventh conference in 2021, office technical work small group activities were added, and the conference was held over two days split into office technical work and skilled labor. With a target of achieving participation of all employees by 2025, efforts were made to raise the level of activities in the region overall and expand the scope of activities through mutual improvement among locations through the conferences.
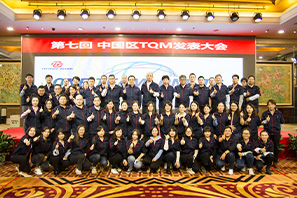
Sales activities aligned with customer needs
Toyoda Gosei sales and other departments meet the demands of customers around the world, growing sales while building good customer relationships. We collect and analyze data on customers’ needs and the issues they are facing, and then work with engineering and other relevant departments in the company to present development plans aligned with those needs to provide products that will satisfy them.