Renewed determination in efforts to face global challenges
Natural disasters due to climate change, including floods from heavy rains and fires resulting from heat waves, have been occurring in all parts of the world. These events have enormous social and economic impacts. Many countries have set targets for CO2 reductions and introduced strict regulations, such as carbon border taxes. Japan has declared “2050 carbon neutrality.” For businesses, this problem cannot be dismissed as a “fire on the other side of the river.” Automakers, given that large amounts of CO2 are emitted over the entire lifecycle of their products, are rapidly shifting to zero emissions vehicles such as BEVs and FCEVs. Their demands for cooperation from suppliers are strong, and we will soon be facing a situation where CO2 reductions are a condition for receiving orders.
Toyoda Gosei first started full-fledged environmental activities in 1993 with the adoption of its 1st Environmental Action Plan, a five-year plan for environmental initiatives. In February 2016, it announced the TG 2050 Environmental Challenge consisting of six aggressive targets, one of which is a clear declaration for a decarbonized society. This marked a turning point, and each department has been making aggressive efforts. They include TG-ESCO activities in which entire plants make regular improvements to reduce energy loss by always turning off power sources during non-production times and switching to energy-saving equipment; reductions in waste and the amounts of water used; and introduction of renewable energy. To achieve carbon neutrality, it will be necessary to combine a number of things such as development of materials that do not emit CO2 and innovative technical developments that will significantly change manufacturing systems. To advance these efforts in parallel, we will incorporate various methods, including cooperation with other companies, and act with a sense of urgency.
Toyoda Gosei specializes in rubber and plastic polymer technology. In moving toward carbon neutrality, we will act with the determination to lead the industry and the Group.
■How we think about environmental activities
■2050 Environmental Challenge
Targets 50&50
Toyoda Gosei again declared “2050 carbon neutrality” at its ESG briefing in April 2021, positioning this as an important management issue. It has also announced its “Targets 50&50,” which sets mid-range targets of reducing CO2 emissions by 50% (compared with 2013 levels) and raising its renewable energy usage rate to 50% by 2030. The Targets 50&50 are milestones that must be reached to achieve carbon neutrality, and the entire Toyoda Gosei Group, including suppliers, is working toward them.
Creating systems for rubber and plastic circulation
Product lifecycle
Achieving 2050 carbon neutrality will require the combination of a number of innovative approaches that enable CO2 reductions over the entire lifecycle of the product, from the procurement of materials and parts that form the upstream aspects of manufacturing all the way through to the disposal stage after products are no longer in use.
A rubber and plastics specialist
Toyoda Gosei has contributed to lighter weight automobiles and to solving environmental problems with its technical abilities and know-how as a manufacturer that specializes in rubber and plastics. Carbon neutrality is an issue that needs to be tackled on a global scale, and we would like to fulfill a social role by achieving decarbonization over the entire lifecycle of our rubber and plastic products. For example, we will take on the challenge of creating cyclical mechanisms for rubber and plastic in collaboration with the plastics industry, such as using naturally derived plastics with low CO2 emissions. In addition, while up to now delivering high quality products at reasonable prices to customers has led to added value, in the coming years we will try to raise product value further by reducing CO2 over the entire lifecycle of each product.
To balance these efforts for the environment while achieving stable growth of the company, we are accelerating the development of products for BEVs and FCEVs, including those that can be used for CASE and MaaS (Mobility as a Service). Toyoda Gosei has many outside directors and other experts specializing in the environment, and we will mobilize all our resources for this while emphasizing speed and effectiveness.
A company-wide cross-over project for corporate activities
Strengthened systems
The Carbon Neutrality and Environment Promotion Division was established in June 2021 to strengthen Toyoda Gosei’s systems for promoting these efforts. The Environmental Committee that is central to these activities was expanded in 2019 to the Global Environmental Committee, which includes the presidents of overseas head offices, and in 2021 the Carbon Neutrality and Environmental Committee. The system for end-to-end efforts has been put in place as a company-wide, cross-functional project from development and design to production. To promote sustainable activities, we are also working to create a corporate culture and personnel with a high environmental awareness.
Becoming “Environmental TG”
Toyoda Gosei’s philosophy of “Boundless Creativity and Social Contribution” is the foundation of our efforts for carbon neutrality. As “Environmental TG,” a leader in reducing CO2 in the field of rubber and plastics, we aim to be a company that contributes to a sustainable society.
■Medium- and long-term scenarios for carbon neutrality
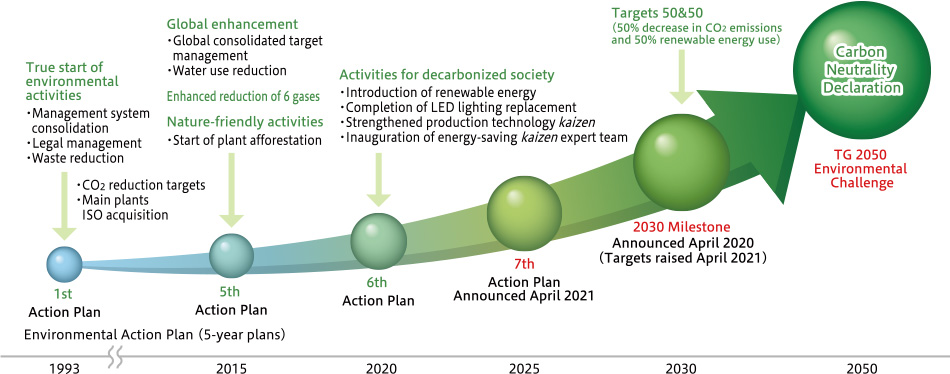
Roadmap for carbon neutrality by 2050
Expanding fields of activity
In fiscal 2020, carbon emissions from Toyoda Gosei’s entire supply chain was 1.55 million t-CO2. Of that, direct emissions from our company’s business activities (Scope 1) were 99,000 t-CO2, indirect emissions from the use of purchased electricity (Scope 2) were 367,000 t-CO2, and emissions other than Scope 1 and 2, from the procurement of raw materials, commuting and business trips, and product use and disposal (Scope 3), were 1.09 million t-CO2.
About five years ago, Toyoda Gosei set down four pillars as activities for bringing CO2 emissions (Scope 1 and 2) related to production at the company down to zero, and has aimed to achieve that target at an early stage. Currently, we have expanded that range to include activities before and after production (Scope 3), which accounts for about seventy percent of our supply chain emissions, to achieve carbon neutrality over the entire lifecycle. We are strengthening and expanding various activities with a deep commitment to reduce CO2 emissions.
Four pillars for our aim of reaching zero
Pillar Ⅰ Daily improvements
In addition to ongoing activities to save energy at plants, members of the Carbon Neutrality and Environment Promotion Division and plant members have worked together for on-site surveys of energy loss, as well as to study improvement methods and implement measures. Examples include the introduction of heat recovery heat pumps to reduce steam loss, and the reduction of pressure loss in compressed air.
Pillar Ⅱ Innovative production technologies
We aim for high value-added plants through innovations on the manufacturing floor, including the design of energy-saving processes and manufacturing methods while thoroughly pursuing production lines that emit as little CO2 as possible. We are also moving ahead with technical innovations such as the prevention of trouble with the use of IoT/AI and the reuse of waste materials.
Pillar Ⅲ Utilities upgrades
We are making systematic upgrades to utility equipment, the source of power used in our production processes, because worn out equipment presents a risk of production problems and has inferior efficiency. We are also replacing heavy oil with LNG as a power source for steam energy, and making other systematic upgrades to low CO2 equipment.
Pillar Ⅳ Introduction of renewable energy
We began installing solar power generation equipment in 2007. Since 2019, we have become more active in introducing renewable energy, such as by standardizing installation of solar power generation equipment in new plants.
■Plan for achieving carbon neutrality
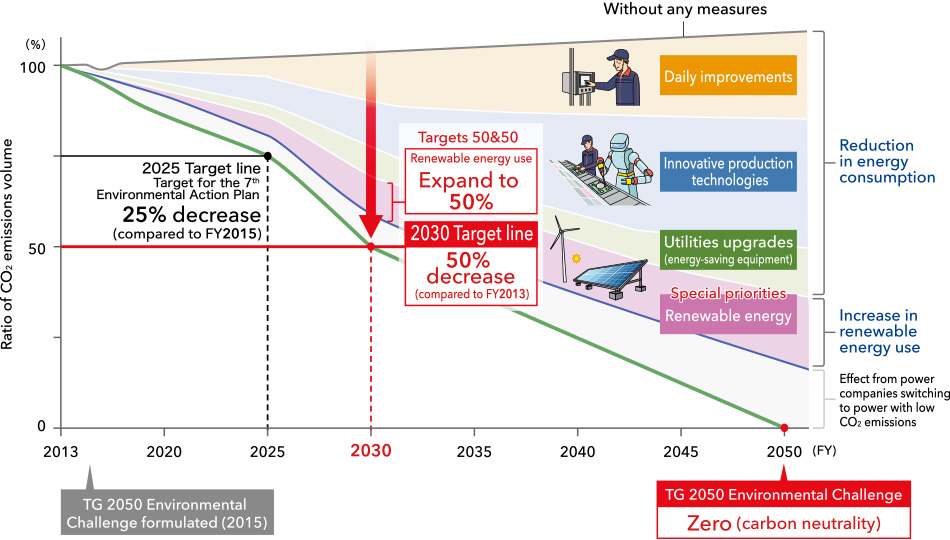
Contributing to zero CO2 emissions with product development that brings together our technical abilities
Up to this time, delivering high quality parts at reasonable prices to customers has led to added value. In the coming years, however, the development of products that can contribute to a recycling-oriented society will be important. Toyoda Gosei is a manufacturer of rubber and plastic products, and we aim to achieve zero CO2 emissions over the entire lifecycle of products by bringing together a number of technological strengths, including material development, lighter weight, process innovations, and 100% recycling. From the stage of purchase of raw materials and parts until disposal.
Challenge of reducing CO2 emissions
【Raw materials】From crude oil-derived to plant-derived materials
Plastic is light and easy to process, and has contributed significantly to lighter weight vehicles. On the down side, it does not decompose easily in the natural environment and if it is burned during disposal it emits CO2. To bring the new added value of “sustainability” to plastics, we are working aggressively to develop plastics that pose a low environmental burden, such as biomass plastic or biodegradable plastics as a new, nonpetroleum resource.
【Core technology】Cellulose nanofiber
Naturally derived cellulose nanofiber (CNF), in which fiber from wood material is extracted and nanosized, is characterized by low density and high rigidity, providing both light weight and strength. It has one-fifth the weight of steel and more than five times the strength. It effectively reduces CO2 emissions thanks to its light weight. It is plant-derived, absorbs CO2 when the plant is growing. Even if it is burned during disposal, CO2 does not increase. With the aim of applying CNF in automotive parts, Toyoda Gosei is developing a composite material that combines CNF and plastic.
【Design】Easy disassembly
When automobiles are scrapped, iron, glass, plastics and other materials are reused by returning them to a raw material state. However, about 140 kilograms of material from each automobile cannot be reused and is discarded. One reason is that these materials cannot be broken down. Toyoda Gosei is therefore reviewing the fixation methods of our parts from the design stage in the upstream manufacturing process, and adopting structures that make them easier to take apart to reduce waste and increase recycling.
【Process】Surface treatment innovations
Painting and plating lines, which involve surface treatment technology that improves designability and appearance quality, emit large amounts of CO2. We are aiming to innovate surface treatment processes, such as switching to plastic materials with outstanding appearance quality that do not require plating.
【Process】Rubber processing innovations
General rubber vulcanization processes need large amounts of steam or heat. We focused on the energy loss that occurs at that time and are trying to create innovative processes for steamless vulcanization, ambient pressure low temperature vulcanization, and no secondary vulcanization.
■Expanding range from our own activities only (Scope 1, 2) to the entire product lifecycle of our products
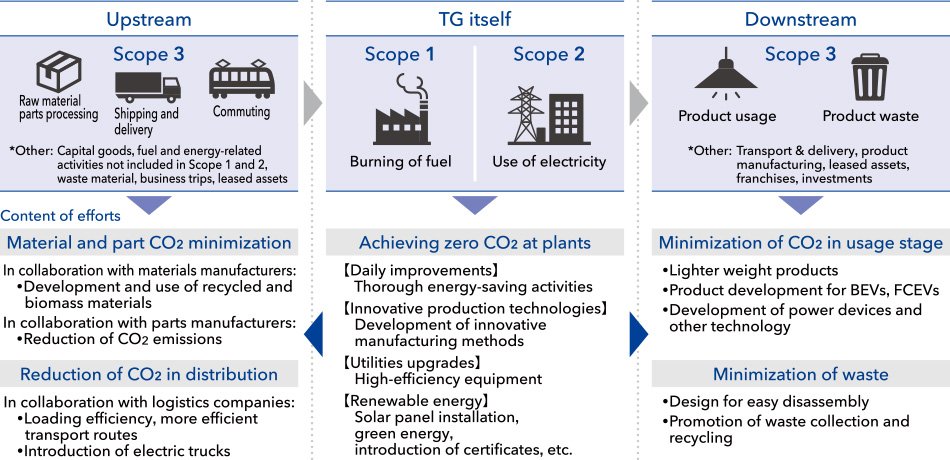
Concrete efforts for carbon neutrality
Product development efforts
Plastic products
We are developing products that have a low environmental impact while also ensuring a profit. For example, by replacing the metal that previously was used in nearly all fuel filler pipes with plastic material, we were able to reduce weight by 50%. Today, we are spreading plastic fuel filler pipe production lines at overseas locations around the globe, contributing to decreased environmental impacts. In the future, we will use the know-how we have cultivated over many years in fuel system parts to develop technologies and products for BEVs and FCEVs. In addition, through onboard products that apply LEDs, another of our fields of expertise, we will contribute to lower electricity consumption in automobiles.
■Product development that contributes to both environmental impact reduction and profits
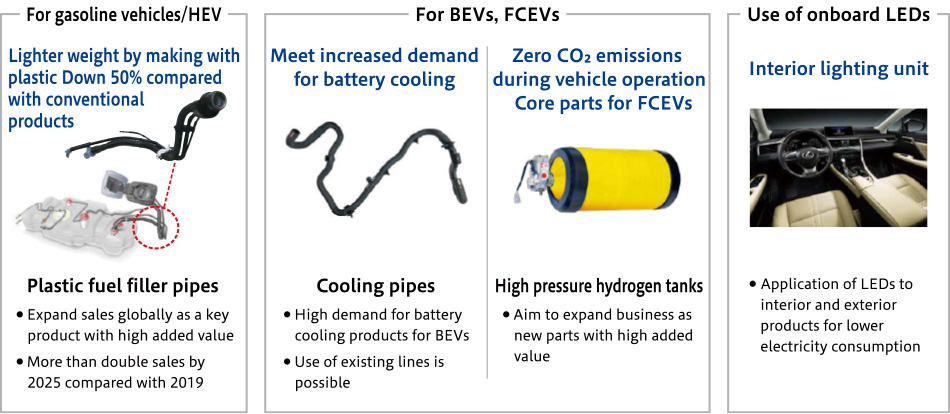
Rubber products
Regeneration of vulcanized rubber has long been considered difficult. However, we developed a practical devulcanization technology for the regeneration of vulcanized rubber about 25 years ago with the purpose of eliminating waste materials that are discharged from weatherstrip production processes at Toyoda Gosei. We are now aiming to further improve the quality of reclaimed rubber and raise recycling efficiency. The key points in devulcanization technology are to apply appropriate energy in the devulcanization process and selectively cleave the cross-links in rubber molecules. We have made innovative modifications that control temperature, compressive force, and shear force by adopting the optimum shape and combination of pieces consisting of screws on two axes.
A dedicated building for the devulcanization (recycling) process was established at the Morimachi Plant in 2021. This has made it possible to cut waste materials of opening trims by more than 40%. We have also developed reuse/recycled products such as fatigue reduction mats, and are minimizing waste by using rubber waste material and remnants to steadily reduce CO2 emissions in the rubber field.
■Rubber recycling with devulcanization technology
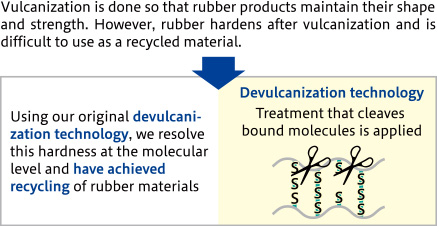
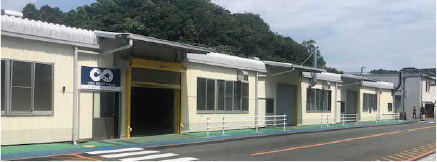
Efforts for zero plant CO2
More compact painting lines
Painting lines are subject to severe scrutiny for appearance quality, for which environmental control is very important. Constant temperature and humidity must always be maintained in painting booths. Because of that, air conditioning equipment has accounted for about 40% of the energy consumption in painting lines.
We have now succeeded in making painting booths more compact by switching the method used to transport materials prior to painting to the painting robots. Switching from a “slider system” to a “turn system + tilt mechanism” that can transport materials in a smaller space has allowed us reduce the booth volume by about half. This smaller size results in a huge reduction in the energy consumed by air conditioning equipment, and has cut CO2 emissions by about 30%. The painting yield is also increased by simplifying the robot posture, leading to higher quality. We are now going to make compact painting booths standard and spread them globally.
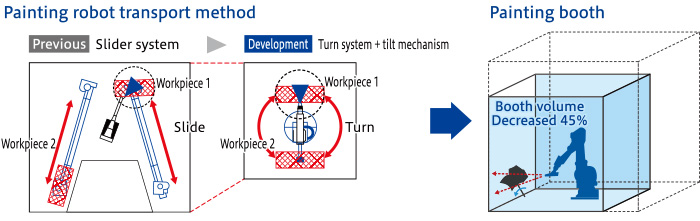
Establishment of vulcanization simulation
In the rubber extrusion process, we previously conducted repeated trials and analyses while changing the time and temperature for vulcanization. We have now established a technology that can simulate this prior to vulcanization based on process and material data. Using this technology, we have succeeded in greatly reducing the number of trials and have been able to reduce the amount of energy needed in starting up a process.
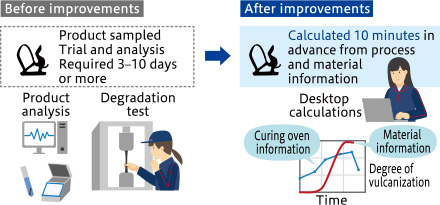
Introduction of renewable energy
Starting with the introduction of solar power at a company dormitory in 2007, we have installed solar power equipment at a number of Group locations. Since 2017, the Environmental Committee has played a leading role, with solar power implementation and investment plans made in the committee. The installation of solar power generation facilities in new plants was standardized in 2019, and is being spread to Toyoda Gosei locations globally. At the Inabe Plant in Japan, wind power equipment has also been installed and CO2 emissions are expected to be cut 800 tons annually from the use of renewable energy.
■Inabe Plant
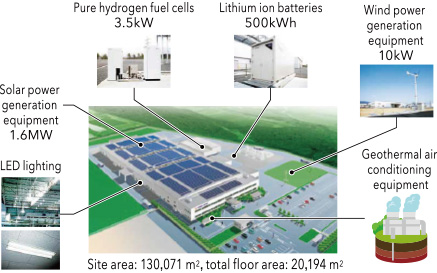
■Toyoda Gosei Memorial Gymnasium ENTRIO
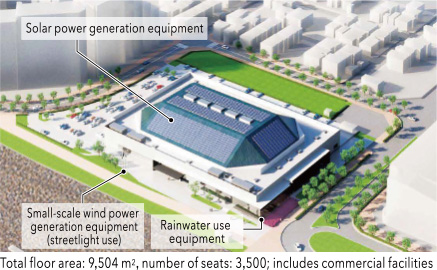