Customer Relations
With priorities on customers and quality, we are working to constantly improve our products and services and our value as a company.
Uniform Global Quality Assurance
Commitment to Quality Assurance
Under our basic quality policy, we guarantee quality at every step from development to production for “Customer First” and “Quality First” principles.
For our quality assurance systems, we have obtained certification under the international standards ISO 9001/ IATF 16949 and have established a quality management system. We are also working to strengthen quality assurance throughout the Group using the Quality System Global Standards*1 as common rules. We pursue quality that meets customer expectations by reliably building quality into new products through our Initial Management System, which checks how well each process is done, from planning to design and production.
- *1 Incorporates the know-how and rules for quality improvement in the Toyoda Gosei Group
■Gate Control by Initial Management System

TQM for a Stronger, Better Company
Based on the basic principles of TQM,*2 we are raising product and work quality and individual and organizational vitality. Company-wide TQM activities are undertaken to create a flexible and resilient corporate character. In addition to our conventional kaizen activities, including Workplace Management Kaizen Activities and Small Group Activities, we are building a new TQM philosophy with the concept of “changing the way we work in anticipation of coming changes,” and sequentially spreading these new TQM activities in the Group.
- *2 Total Quality Management
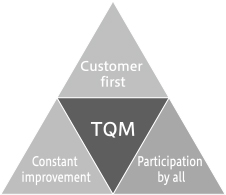
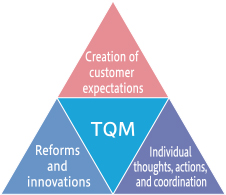
■TQM Activities at Toyoda Gosei
Level | Activities |
---|---|
Manager | Workplace management kaizen activities |
Office, technical workers | Small group activities (group kaizen activities) Activities to improve practical abilities (engineering work) in statistical quality control (SQC) and artificial intelligence (AI) |
Skilled workers | Small group activities (QC Circle activities) |
Development of Human Resources for Future Business and Environmental Changes
We established the Quality Learning Center as a place to foster a mindset in which all members of the Toyoda Gosei Group, including suppliers and overseas locations, can think and act in a “Customer First” and “Quality First” manner. In addition to the company's quality history and examples of quality kaizen that embody the TG Spirit, we use this as a place to repeatedly learn about initiatives as we move toward the future.
In addition, during “Global Quality Month” in November each year, everyone makes a “Declaration of Thought and Action” in their position and role. Through this and the establishment of regular opportunities for everyone to reflect on their own actions, we try to firmly establish the “Customer First” mindset.
Training Personnel with Digital Analysis Skills
With the recent utilization of big data and the rapid expansion of DX, the ability to analyze data has become an essential skill. We are strengthening the practical education, including industry-academia collaboration,*3 of people who can use statistical quality control (SQC) and machine learning (ML).
- *3 Experts from Shiga University and the Toyota Group serve as instructors
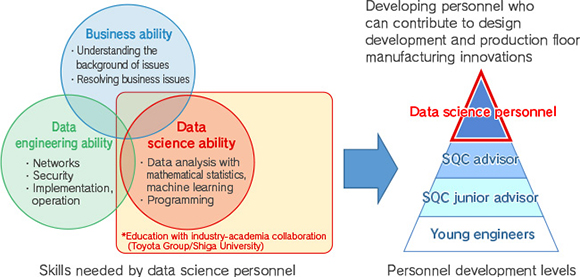
Quality Learning Center Established to Cultivate a Quality Mindset
All members of the Toyoda Gosei Group, including suppliers and international locations, learn repeatedly about quality. We have established a Quality Learning Center to cultivate a mindset of thinking and acting with a customer-first and quality-first approach. In addition to showing examples of past problems, exhibitions convey the company history of placing importance on quality, examples of quality improvements implementing the TG Spirit, and efforts for the future.
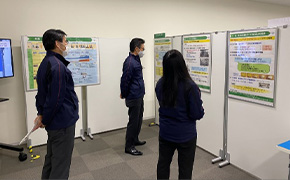
7th “China TQM Conference” Held
In China, where recovery from the coronavirus epidemic came relatively early, small group activity conferences have continued. The sixth conference was held online in 2020 and the seventh conference was held in person in the Zhangjiagang area in 2021.
From the seventh conference in 2021, office technical work small group activities were added, and the conference was held over two days split into office technical work and skilled labor. With a target of achieving participation of all employees by 2025, efforts were made to raise the level of activities in the region overall and expand the scope of activities through mutual improvement among locations through the conferences.
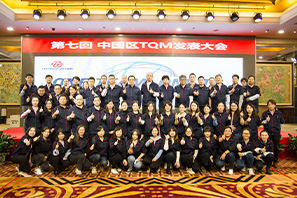
Manufacturing Quality Assurance and Continuous Improvement Activities
In order to deliver safe and secure products to our customers around the world, we are executing defect-free process completion centered on production processes for safety parts, which are directly related to the basic performance (running, turning, and stopping) and safety of vehicles. Audits and improvements by certified auditors are also conducted for safety part production processes.
Ongoing “Quality Assurance Declaration Activities”
We cultivate a workplace culture of continuous improvement and have conducted “Quality Assurance Declaration Activities” since 2012 with the aim of creating manufacturing floors that can cope well with changes. We identify issues from the three angles of developing human resources, developing processes, and preventing recurrences, and then conduct kaizen . At the stage when we achieve our targets, the supervisor gives an “Assurance Declaration” to the company president on-site. With the aim of quality that will earn the trust of the customers globally, we undertake this activity with the participation and concerted effort of the entire Toyoda Gosei Group.
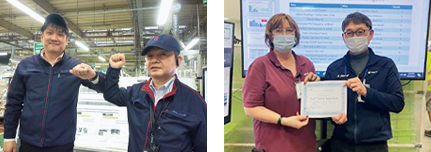
Sales Activities Aligned With Customer Needs
Toyoda Gosei sales and other departments meet the demands of customers around the world, growing sales while building good customer relationships. We collect and analyze data on customers’ needs and the issues they are facing, and then work with engineering and other relevant departments in the company to present development plans aligned with those needs to provide products that will satisfy them.