Build circular and decarbonized societies
- HOME
- Areas of focus
- Build circular and decarbonized societies
To achieve carbon neutrality and a circular economy, Toyoda Gosei has set the targets of zero CO2 emissions and minimizing waste by 2050 (TG 2050 Environmental Challenge). In moving toward these goals, we are leveraging our expertise in rubber and plastics such as material compounding and application technology. We divide the product lifecycle into four phases (materials, design, manufacturing, recovery/recycling), and are making specific efforts for each phase.
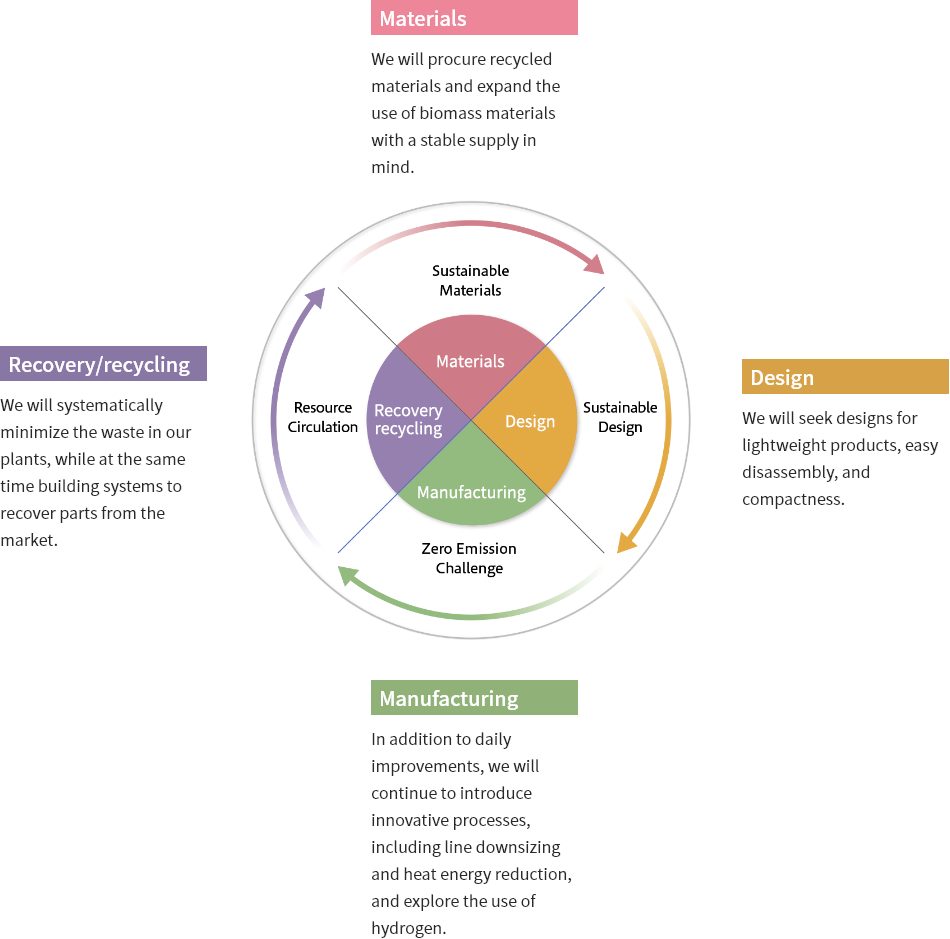
Technical development roadmap
We aim to take the lead in carbon neutrality for automotive parts by making significant changes to materials development, design, manufacturing (production technology), working in tandem with suppliers, and various other efforts. Our initial efforts are in the area of material recycling, including developing recycling processes for rubber and plastic waste and making products with recycled materials. Other efforts include material-saving products to reduce material use, energy-saving production processes, and replacement with biomaterials.
-
01Recycled rubber
Rubber desulfurization technology
Rubber is a difficult material to recycle because it goes through the process of vulcanization in which molecular bonds* are formed to give it greater elasticity for commercial use. Using original technology, we have succeeded in regenerating high quality rubber in a shorter time with a desulfurization process wherein those molecular bonds are cleaved to return the material to a state in which it can be used again as a raw material.
*In vulcanization, rubber raw material is mixed with sulfur compounds and heated, forming cross-links between the macromolecules in rubber and the sulfur compound.
-
02Biomaterials
CNF-reinforced plastic
To raise the environmental value of our products, we are introducing various biomaterials using our strengths in material technology. One is the use of cellulose nanofiber (CNF)* as a reinforcing material mixed in plastic, which can make products lighter in weight and enables recycling in automotive parts. It is useful material in moving toward decarbonization and a recycling society. One issue that needed to be overcome for the practical use of CNF-reinforced plastic is that when CNF is mixed in the general-purpose plastic (polypropylene) that has been used in automobile exterior and interior components, its impact resistance is decreased. With our compounding design and kneading technology we have successfully raised the impact resistance of CNF-reinforced plastic to a level that can be used in automotive parts.
*Cellulose nanofiber is a plant material that has one-fifth the weight and five times the strength of steel.
-
03Use of new resources
Hydrogen storage
The features of hydrogen include that it can be manufactured from various resources, does not generate CO2 when used as fuel, and it can be used as a medium to store, move, and use renewable energy. To increase the use of hydrogen in society, there are growing needs to store large volumes of hydrogen more efficiently. Toyoda Gosei continues to develop its hydrogen tank technology while also developing hydrogen tanks that are compact and can hold large volumes of hydrogen.
-
04Material-saving design
Thinner components that contribute to vehicle interior spaces suited to BEVs
With the aim of increasing automobile fuel efficiency through lighter weight products, Toyoda Gosei has long been making efforts to reduce the materials used in its products by leveraging its expertise in rubber and plastics. This includes decreased material thickness, greater compactness, fewer parts, lower specific gravity, and foaming. In recent years we are using these technologies to develop thinner and more compact cockpits with the aim of achieving more spacious vehicle interiors compatible with the switch to BEVs. We are also developing and proposing airbags, registers and more that can be used with thinner instrument panels.
-
05Easy disassembly design
Driver-side airbag products
Pads and metal used to be put together with rivets. However, if there was a problem in some element prior to completion, the product could not be taken apart and the whole thing had to be scrapped, including elements with no problems. By switching to a fixation method that does not diminish product quality and a structure that allows easy disassembly, we have made it so that each element (plastic pad, cloth, metal) can be taken apart for easy recycling.
-
06Energy savings
More compact painting booths
We have introduced a new painting robot that increases yield with a turntable system, achieving a 45% reduction in space. That has resulted in a 30% decrease in CO2 emissions while also improving productivity and reducing environmental impact. In addition, a new structure for the product fixture that can change the orientation has enabled the product to be always sprayed from above to below. By this, the painting robot’s range of motion is decreased and paint particles are kept down. Maintenance work has also become easier.
-
07Waste heat utilization
Use of factory waste heat
Thermoelectric power generation is the power generation method of converting heat energy into electric energy without emitting CO2. In August 2021, Toyoda Gosei invested in E-ThermoGentek Co., Ltd., a startup that possesses original thermoelectric power generation technology, and we have been developing ways to effectively use the waste heat generated in production processes and elsewhere.