Taking on Rubber Recycling with Original Technology
2024.02.21
- HOME
- Features & Topics
- Taking on Rubber Recycling with Original Technology
To protect the environment, many of the materials around us, including paper, plastic and metals, are increasingly recycled. Rubber is different; it cannot be easily recycled and nearly all waste rubber is incinerated, emitting CO2. Rubber needs to be returned to a raw material state and reused.
Toyoda Gosei has among the world’s largest shares in weatherstrips, automotive rubber products that prevent rain, dust and noise from entering vehicle cabins. With its original devulcanization technology for rubber waste materials, the company will lead the rubber industry in recycling on the way toward decarbonization.
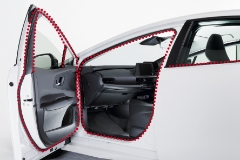
01Achieving high quality reclaimed rubber with original devulcanization technology
To return rubber products to a raw material state, a process is needed to break the chemical bonds that serve to give rubber its elasticity. The process is called devulcanization. The method generally used in devulcanization is the “pan process”, in which rubber and a reclaiming agent are mixed, and may be likened to boiling the material in a kiln. However, because it requires high temperature, high pressure, and long times, it causes significant damage to the material and quality deteriorates.
With its environmental awareness in the 1990s, Toyoda Gosei developed an original devulcanization technology while also pursuing high quality. It has achieved recycling of rubber waste materials generated in its manufacturing processes. By applying the optimum heat and pressure so that only cross-links are cleaved as the rubber waste material is extruded with two screws, material with quality close to that of unprocessed rubber can be reclaimed in a short time and with good efficiency.
■What is devulcanization?
In the molecular structure of rubber there are main chains (carbon-carbon (C-C) bonds) and the chemical bonds formed in vulcanization (carbon-sulfur (C-S) and sulfur-sulfur (S-S) bonds). With application of appropriate energy, only the bonds formed in vulcanization are cleaved, restoring the properties of rubber.
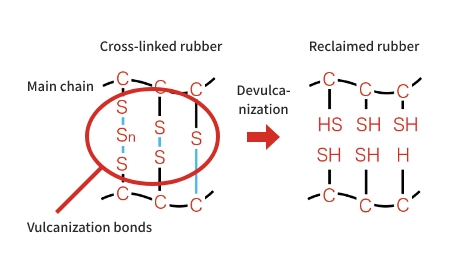
■Mechanisms of Toyoda Gosei’s devulcanization technology
Two screws are turned at high speeds, giving the energy needed for devulcanization. By optimizing the shape of the screws, rotation speed, temperature setting and other factors, the molecular bonds in rubber are selectively cleaved.
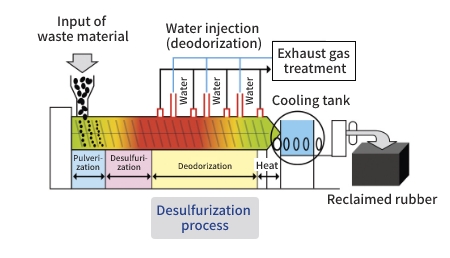
■Quality comparison of reclaimed rubber (comparison with pan process)
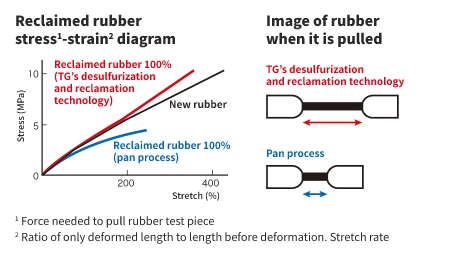
02Controlling the odor of reclaimed rubber with deodorization technology
One of the biggest issues with reclaimed rubber is the smell. A strong smell is generated from the mixing of more than 200 odorous components—the smells from the raw materials and chemicals themselves, plus the smells emitted when the chemical reactions occur in devulcanization. In nearly all cases, general recycled rubber is used outdoors, such as by being mixed into asphalt. Toyoda Gosei focused on the odorous components that are unpleasant to humans, and established a deodorization technology that dissolves and disperses these components in water and then expels them together with steam.
In an experiment that quantified the strength of odors, the result obtained with Toyoda Gosei’s process was less than one-tenth that with the pan process. The company’s challenge going forward is to not only eliminate odors generated in manufacturing processes but also to develop a devulcanization and reclamation process that does not generate foul odors.
■Deodorization technology mechanism
Attention was directed to that fact that odorous components bind easily with water. By injecting water into the devulcanization reaction, the odorous components are dissolved in water and then expelled together with steam.
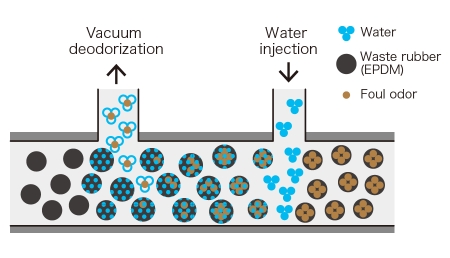
■Comparison of reclaimed rubber odor
Analysis by thermal desorption of the volume of gas volatilized from reclaimed rubber. A relative assessment was made with Company C as 100.
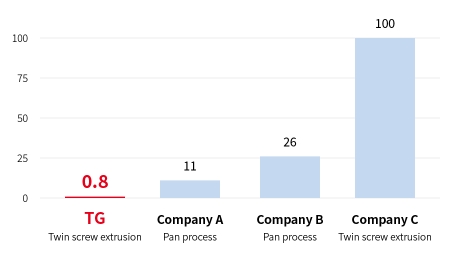
03Acquisition of international certification that leads to greater recycling
Toyoda Gosei’s Morimachi Plant, the company’s main plant for weatherstrips, has acquired ISCC PLUS certification.3 This is an international certification for sustainable products manufactured with recycled materials. This was the first time the certification had been received in Japan for the use of in-house waste material.
Toyoda Gosei has previously mixed reclaimed rubber into some of its products, but the blending ratio has never gone beyond several percent. As the company’s devulcanization technology and deodorization technology evolves, it plans to raise the blending ratio to 20%, which can reduce CO2 emissions per weatherstrip (opening trim) by 10% compared with new material. Application of the mass-balance approach used in ISCC certification and the market launch of products with high environmental value will also make Toyoda Gosei’s devulcanization and reclamation technology more widely known. This may well lead to wider use of recycled rubber.
3 International Sustainability & Carbon Certification (ISCC) is a program the certifies the sustainability of biomass and recycled materials.
■What does it mean to use the mass balance approach?
Products can be introduced on the market as products with high environmental value by theoretically concentrating the blending ratio for reclaimed rubber products into a fixed number of products.
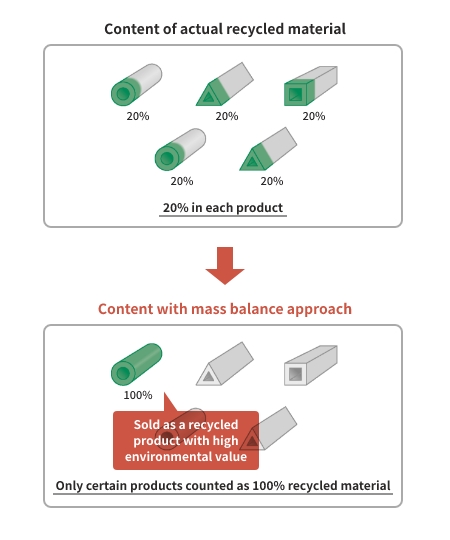
04Moving toward a society that can recycle rubber resources
A second devulcanization line is put into operation in the Morimachi Plant in FY2023. This enables reclamation of 1,200 tons of synthetic rubber waste annually. Toyoda Gosei is currently investigating a plan to spread devulcanization and reclamation lines at its overseas locations as well, with the aim of local production and local consumption of rubber waste materials. The company will deepen collaboration with automakers with the aim of establishing a recycling system to collect rubber from end-of-life vehicles in the future.
Toyoda Gosei has also succeeded in devulcanization and reclamation of natural rubber at the experimental level, and is moving toward early commercialization.
Voice of developer
Aiming for a rubber recycling business that involves all of society
Toyoda Gosei’s roots go back to the Rubber Research Department of Toyoda Automatic Loom Works, and its knowledge of polymer materials cultivated over many years is one of its key strengths. Momentum for the use of recycled materials is increasing with the recycling rules for end-of-life vehicles centered on Europe (ELV Directive) and with a view toward future rubber recycling needs in the automobile industry, Toyoda Gosei will lead the industry in polymer material technology and contribute to a decarbonized society.
Kiyokazu Sodeyama, Group Manager, Material Engineering Division