Technology that supports the spread of FCEVs.
Working toward decarbonization with high pressure hydrogen tanks
2023.03.23
- HOME
- Features & Topics
- Technology that supports the spread of FCEVs. Working toward decarbonization with high pressure hydrogen tanks
Against a background of rapid climate change due to growing CO2 and other greenhouse gas emissions, battery electric vehicles (BEVs) and fuel cell electric vehicles (FCEVs), which do not emit CO2 during operation, are expected to come into wider use. FCEVs that run on hydrogen will play a role in encouraging the use of hydrogen in society overall. Toyoda Gosei's plastic technology supports the extended driving range and lower cost that is essential to the more widespread use of FCEVs.
01Mirai, third tank
FCEVs run on the electricity generated when the hydrogen in the tank reacts with oxygen in the air. To extend its driving range on a single refueling, Toyota’s second generation Mirai FCEV, launched in 2020, has three hydrogen tanks, one more than the first-generation Mirai. Toyoda Gosei used the high pressure hydrogen tank technology it had cultivated over more than 20 years in producing the third tank, which is loaded in the rear of the Mirai.
FCEV mechanism
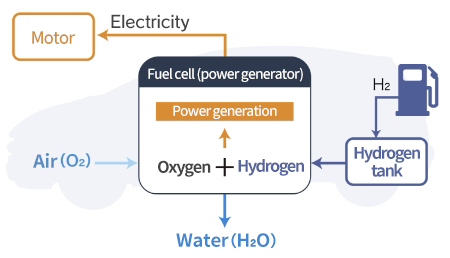
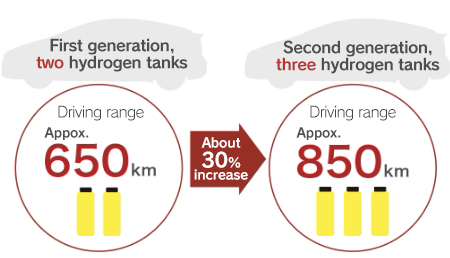
02Storing larger amounts of hydrogen
The role of high pressure hydrogen tanks is to efficiently store hydrogen. These tanks have a three-layered structure to increase their airtightness and pressure resistance. The innermost layer is a plastic liner (A) that serves as a plastic capsule with a special molecular structure to minimize the permeation of hydrogen, the smallest molecules that easily pass through materials. Here, hydrogen gas is compressed to 700 atm and stored. The plastic tank is wrapped with multiple layers of carbon fiber reinforced plastic (CFRP) (B), a material also used in airplane bodies because it is lighter and stronger than steel, so that it can withstand pressure equal to that at a depth of 7,000 meters in the ocean. The outer layer is a made by wrapping with glass fiber reinforced plastic (GFRP) (C) to protect the CFRP pressure resistance layer.
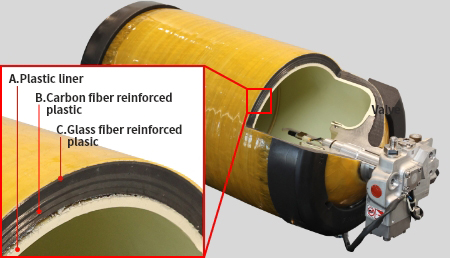
This tank for the second-generation Mirai was developed jointly by Toyota Motor Corporation and Toyoda Gosei, and has higher performance than the tanks in the first generation Mirai. It maintains strong pressure resistance with innovations in the structure of the pressure resistance layer and production method, while also minimizing the pressure resistance layer, the thickest of the three layers, to increase the internal volume. This raised the hydrogen storage efficiency (the ratio of amount of hydrogen stored to the tank mass) by about 10%. The CFRP winding method was devised to provide the greatest strength with the use of computer simulation technology. The plastic liner was also made more airtight and thinner by reviewing the materials and construction method.
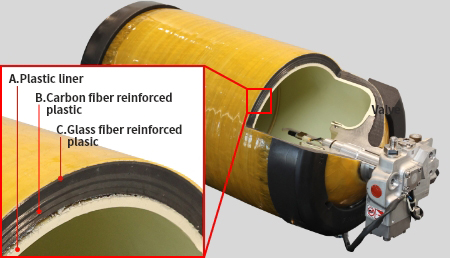
03Improving productivity
Productivity was also raised by shortening the process time. There are five processes in producing high pressure hydrogen tanks: (1) molding, (2) welding, (3) filament winding (FW), (4) curing, and (5) inspection. In the laser welding process (2) for the plastic liner, we switched from laser welding to heat welding (non-contact infrared welding), greatly reducing the process time. With this change in the welding method, we also succeeded in lessening the reduction in strength and stretch of the plastic liner from welding defects, achieving a lower defect rate and more stable welding quality. Improvements were also made in the FW process (3) to wrap the tank with CFRP and GFRP, and the subsequent curing process (4), in which the thermosetting resin (epoxy resin) contained in the CFRP and GFRP is heated and cured, which are the most time-consuming processes. An original control program was developed for faster winding of CFRP to shorten the winding time. The curing time was also significantly shortened by modifying the additives to the epoxy resin.
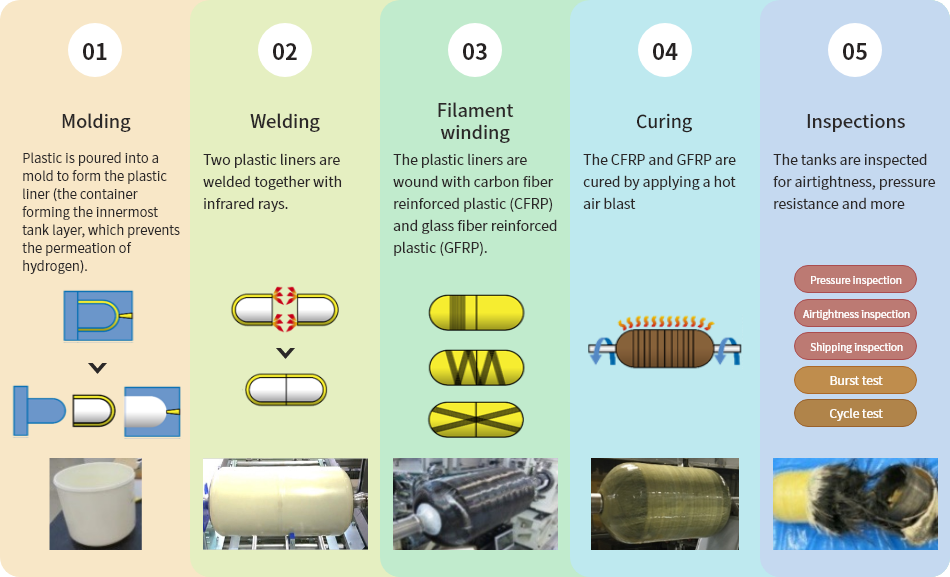
04Taking on further challenges to promote the use of hydrogen
Toyoda Gosei began producing large tanks for commercial trucks in October 2022. We will increase the variations in terms of size and resistance performance with a view to tanks used in various forms of mobility, not only commercial vehicles but also motorcycles, ships, and railways. At the same time, we will work to develop portable tanks that will make it easy to carry hydrogen even in the home, and materials for compact high capacity tanks.
Voice of developer
High pressure hydrogen tanks are the culmination of past knowledge and technical innovation
Mass production of high pressure hydrogen tanks is not something that can be achieved overnight. We began developing the high pressure hydrogen tanks used in FCEVs in 2002, but before that we had begun developing fuel tanks for natural gas (CNG) automobiles in 1995. It is these many years of technical innovation and accumulation of knowledge that made it possible for us to create high pressure hydrogen tanks that are safe and high-quality.
There were ups and downs in developing these tanks, but the foresight of management that made the decision to continue development and the spirit of the engineers who did not give up even when they felt disheartened has been passed down to us. With this spirit in mind, I want to continue working to develop tanks that can raise the level of on-board freedom.
Nobuaki Kameda, General Manager, FCEV Business Planning and Engineering Div.